
Au cours des trois dernières années, la ferme am Eulenbruch (www.boese-farm.de) à Hespe, en Basse-Saxe, a mis l'accent sur la gestion de l'énergie. "Entre-temps, l'autosuffisance est devenue la chose la plus importante pour moi. Elle me donne la tranquillité et la sécurité de planification", constate Hannes-Friedrich Böse. Ce diplômé d'État en gestion agricole voulait être indépendant du marché mondial en matière d'énergie. "Je voyais mon avenir dans le fait de me spécialiser dans les matières premières renouvelables de la région et d'en faire profiter les habitants de la région. J'ai réussi à mettre en place cette base de planification et de travail", se réjouit le jeune homme de 32 ans, qui est tout à fait conscient que l'énergie devient de plus en plus rare et chère. Dans cette branche, l'accent est mis sur la production et la commercialisation de plaquettes de bois et, depuis août 2022, de granulés de bois - produits par l'installation de granulation de l'entreprise Ecokraft.
Hannes-Friedrich Böse a repris en 2020 l'exploitation de ses parents dont l'histoire remarquable remonte à 1620. L'exploitation mixte conventionnelle pratique l'agriculture et l'engraissement de volailles. Avec la reprise de l'exploitation, le jeune homme s'est également concentré sur les copeaux et les pellets de bois en tant que combustibles de qualité et alternative écologique aux sources d'énergie traditionnelles.

Figure 1 : Hannes-Friedrich Böse avec ses copeaux de bois
Depuis neuf ans, l'exploitation dispose d'un chauffage à plaquettes avec un réseau de chaleur interne. Outre la propre forêt de l'entreprise, les copeaux proviennent principalement de communes et de forêts privées, régionales, départementales et nationales situées à 20 km de l'entreprise. L'extraction se fait en collaboration avec la société JB Erdbau, dirigée par son frère Jan-Christoph. Tous deux se partagent le démarchage des clients. Ensuite, c'est l'entreprise Erdbau qui produit et livre la marchandise. Outre l'utilisation des résidus de bois, les grumes qui ne peuvent plus être utilisées comme bois de construction servent également de base.
La surface de stockage humide de l'exploitation peut accueillir environ 2000 m3 de copeaux. L'entreprise traite actuellement 30000 m3 par an de la classe de qualité G 30 à G 50. La marchandise humide repose au maximum une semaine avant d'être mise à sécher. Un chargeur télescopique la soulève dans la trémie de stockage qui mène au séchoir rotatif à poussée de la société Riela. Le séchoir continu mesure 14 m de long et 2 m de large et travaille avec une puissance de séchage de 400 kW pour sécher les plaquettes de bois de 55 pour cent à 15 à 20 pour cent d'humidité. Dans le séchoir à retournement de poussée, de l'air à 70 °C est soufflé à travers le matériau, les plaquettes étant constamment retournées par des râteaux. L'air humide est aspiré, la poussière est filtrée et de l'air propre est évacué vers l'extérieur. "Le séchage est entièrement automatisé et fonctionne en continu depuis deux ans et demi, 365 jours par an, en autarcie. Nous ne remplissons la trémie que le matin et le soir", informe le chef d'exploitation.

Figure 2 : Remplissage du séchoir à tambour rotatif
Chaque jour, 150 m3 de copeaux de bois sont séchés. En moyenne, 100 m3 sont nécessaires par jour - 50 à 60 m3 pour les besoins propres, le reste étant destiné à la commercialisation. Les plaquettes prêtes à l'emploi sont stockées dans le hall jusqu'à ce qu'elles soient commercialisées ou transformées pour des clients privés et industriels ainsi que pour des centrales thermiques.
Début octobre, le séchoir permettra de sécher du maïs pendant deux mois à deux mois et demi - 3500 tonnes au total. 700 tonnes sont du maïs produit par l'entreprise et le reste se répartit entre le séchage à façon et la marchandise achetée et revendue par l'entreprise commerciale de produits agricoles certifiée QS. Le maïs est séché de 30 pour cent à 15 pour cent d'humidité et commercialisé prêt à être stocké et transformé à des usines d'aliments pour animaux dans un rayon de 80 km.
Afin de disposer d'un certain tampon pendant cette période, on fait sécher et on stocke auparavant suffisamment de plaquettes de bois en réserve. Ensuite, le séchoir est nettoyé et les outils du séchoir sont remplacés par des plaquettes..
Auparavant, les usines de pellets étaient également approvisionnées en copeaux de bois. "Puis j'ai eu l'idée de prendre ce rail en main moi-même et de m'en faire une autre source de revenus", raconte Hannes-Friedrich Böse. En cherchant une possibilité, il est tombé sur la société Ecokraft sur Internet, s'est beaucoup informé et a finalement fait affaire avec cette entreprise spécialisée. DL'agriculteur a d'abord pensé à une installation simple, mais il a finalement opté pour une installation duo avec une capacité horaire de 500 à 600 kg. "J'ai pris un certain risque, mais j'ai vu qu'il existait un marché pour ce type d'équipement et, a posteriori, c'était une bonne décision", révèle l'entrepreneur. Ce qui a fait pencher la balance en faveur d'Ecokraft, c'est la possibilité de granuler différents matériaux avec cette installation. "Qui sait comment le marché va évoluer. Avec la filière correspondante, je peux réagir de manière flexible et ainsi granuler du foin, de la paille ou de la laine de mouton", estime le jeune homme de 32 ans.

Figure 3 : Installation de granulation Ecokraft DUO.
Grâce à la situation du marché au cours des dernières années, une clientèle a pu être rapidement constituée et les affaires avec les granulés de bois se portent très bien jusqu'à aujourd'hui. Les avantages des pellets : ils peuvent être transportés, stockés et déversés, ils sont peu encombrants et nécessitent peu de travail, ce qui les rend attrayants pour les particuliers.
La phase de démarrage avec l'installation de granulation a été quelque peu turbulente, mais en collaboration avec le fabricant, les bonnes filières ont été rapidement trouvées et le matériau de départ optimisé pour finalement tirer le meilleur parti de la machine. "J'apprécie le bon service ainsi que les interlocuteurs compétents et sympathiques avec un contact d'égal à égal", confirme Böse.
L'installation de granulation se trouve dans la grange à céréales d'une capacité de stockage de 600 tonnes. Les processus et le déroulement sont désormais bien rodés et nécessitent peu de pièces de rechange. Environ 15 pour cent des copeaux sont transformés en pellets, ce qui représente 5 à 6 tonnes par jour. L'installation fonctionne actuellement 220 jours par an et 5 m3 de copeaux produisent une tonne de granulés.
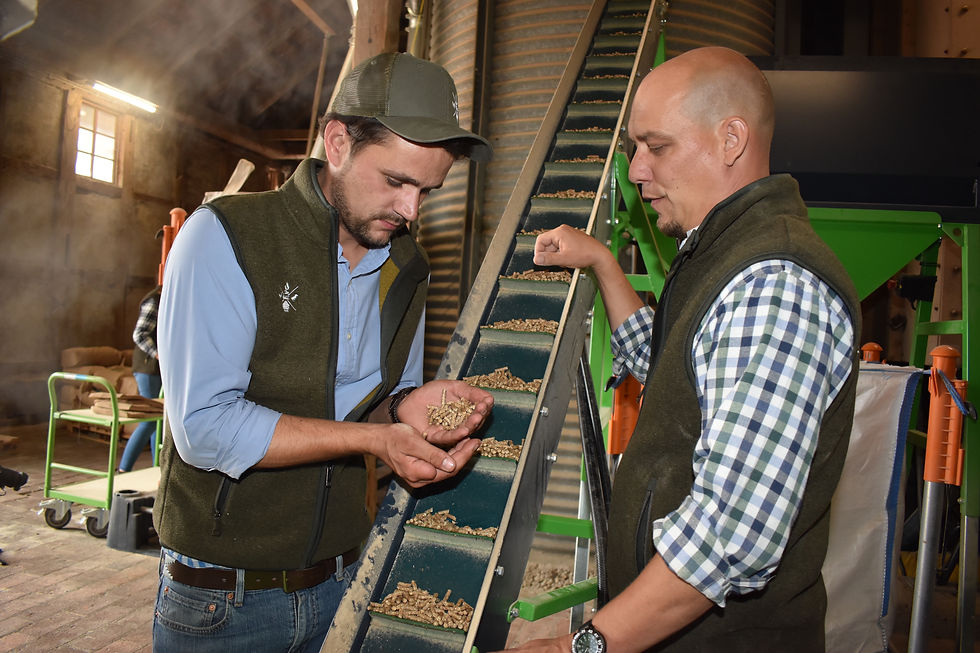
Figure 4 : Hannes-Friedrich Böse avec des granulés d'énergie frais provenant de l'installation de granulation Ecokraft DUO.
Les copeaux sont amenés à l'installation Ecokraft à partir d'une trémie de stockage par un tapis roulant dans le broyeur, qui les réduit à 4 mm. Ensuite, le matériau poursuit sa route vers la trémie de stockage. Avant le pressage, de l'amidon de maïs est ajouté, ce qui rend les pellets brillants et durs et réduit la dépense énergétique. Dans la presse, la matière première est transformée en pellets sous haute pression et haute température. Ceux-ci sont transportés plus loin au moyen d'un tapis roulant et, après un tamisage des petites
particules, ils arrivent dans les silos en hauteur via un élévateur.
Enfin, les pellets sont conditionnés dans des sacs en papier de 15 kg et achetés par les clients grâce à un système de consigne - exclusivement par des clients privés de la zone de chalandise de la matière première, qui achètent de dix sacs à 15 tonnes. "Nous atteignons ainsi la régionalité également dans le secteur de l'énergie", ajoute l'agriculteur. Son idée de système de consigne est née lors du remplissage d'une trémie et est très bien accueillie par les clients. Ceux-ci rapportent les sacs, qui sont utilisés jusqu'à trois fois, et reçoivent un crédit pour la prochaine commande. "Je ne gagne rien en faisant cela, mais la notion de durabilité me tient à cœur", explique l'homme d'affaires, pour qui il est important d'avoir des relations équitables avec ses clients, selon la devise "vivre et laisser vivre".

Figure 5 : Hannes-Friedrich Böse et ses produits à granulés énergie
Avec quatre employés à plein temps, Hannes Friedrich Böse gère les tâches qui l'attendent.
"La décision de se lancer dans la production de granulés était juste et bonne. Ensemble, en combinaison avec le photovoltaïque et la centrale de chauffage à biomasse, nous atteignons l'autosuffisance énergétique et donc la compétitivité à l'avenir", explique Böse, qui gagne ainsi en sécurité de planification.
Grâce à des investissements durables, il a réussi à atteindre l'autosuffisance thermique et électrique au sein de l'entreprise. La centrale de cogénération à bois est une centrale de cogénération à bois et à gaz qui transforme la biomasse ligneuse en gaz combustible. Un générateur le transforme ensuite en énergie électrique. La chaleur résiduelle du procédé est utilisée dans le propre réseau de chaleur pour alimenter les bâtiments de l'entreprise et les habitations ainsi que l'installation de séchage du bois. Grâce à la centrale de cogénération, la production d'énergie est garantie indépendamment des conditions météorologiques et du vent

Figure 6 : Hannes-Friedrich Böse et ses collaborateurs dans sa ferme Eulenbruch
Depuis deux ans, Hannes-Friedrich Böse et son amie Luisa ouvrent le fournil historique, vieux de 170 ans, pour des mariages civils et libres. Cette offre est volontiers acceptée et c'est ainsi qu'environ 30 mariages ont lieu chaque année. Sur demande, un service de restauration est également mis à la disposition des invités dans le jardin idyllique.
Sun projet pour l'avenir : "Développer la commercialisation, gagner des nouveaux clients et mettre en place un réseau de chauffage local pour les bâtiments privés et commerciaux dans les environs"
Voir le site de Farm am Eulenbruch: www.boese-farm.de
- Helga Gebendorfer -